Kata is a Japanese term referring to structure or routine and its purpose is ongoing improvement: following the routine is a practice and it allows you to get better at whatever it is you're doing. When applied to business, it's divided into the improvement kata, which is the four steps your organization can follow to make improvements and the coaching kata, which is the steps taken by leadership to help employees implement the improvement kata.
This is a systematic, scientific approach that can be used to create a culture of safety in your workplace, reduce accidents and injuries, improve morale and productivity and save money.
The 4 Step Improvement Kata
The four steps help you see where you need to improve and create a plan for that improvement.
Step 1: Understand the Direction
What is it that you're all working toward? In terms of safety, it may mean following all OSHA regulations, lowering your injury rate and having 100 percent employee participation in safety checks and risk reporting. Outline your goals in specific terms. Start by revisiting your company mission statement or safety policies.
Step 2: Understand the Current Condition
This involves careful observation—an internal safety audit may be warranted, so you can identify your weak areas. This is not a time for judgment or even action: it's simply a time to make detailed notes about the people and activities and get a thorough understanding of how things are.
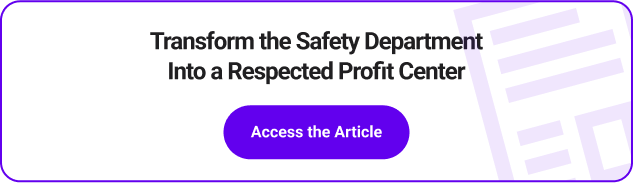
Step 3: Establish the Next Target Condition
During this step, you're not outlining how to improve, you're simply identifying your desired condition. This isn't necessarily the goals you came to understand in Step 1. It's more of a look at each individual condition and how you'd like that to be.
For example, if in Step 2 you discovered a cord lying across a walkway, your target condition for that specific situation would be to have the cord out of the walkway so no one trips over it.
Step 4: Work Toward the Target Condition
This is a process of experimenting with solutions and recording results so you can see what works and what doesn't. Use Plan-Do-Check-Act (PDCA) cycles to try different methods and explore how you've learned from them. Add photos and post your records so the team can see what's being done and how it's changing the workplace for the better. It's not about immediate perfection, but about small improvements on a daily basis that add up to big changes over time.
This is where the coaching kata comes in. Leadership serves in a mentoring role to help employees develop the problem-solving skills to work through the improvement kata. With ongoing feedback and direction, employees build confidence, knowing they're free to innovate and find solutions that benefit the entire organization.
As a coach, help your employees identify obstacles between the current condition and the target condition. Focus their attention on one obstacle at a time, tackle it step-by-step, then reflect on the effectiveness of the solution and what you learned from solving the problem that way.
Tools for Implementing the Improvement Kata
While new processes can seem overwhelming, having the right tools makes them simpler and more likely to be adopted by the entire organization. Audit Inspection software, for example, allows you to efficiently inspect your workplace and take detailed notes about areas for improvement. Health & Safety Management software makes incident (and near-miss) reporting easy for all employees and gives you a place to track behavior-based safety and manage your targets. This empowers the team to get involved and own their roles as you all work together to create a safer working environment.
We have the turn-key EHS and e-learning software solutions you need to implement your improvement kata and generally maintain a safe, compliant workplace. Contact us to learn more.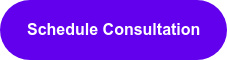
**** If you found the post helpful please like and share *****