Stop Work Authority (SWA) is a program designed to provide employees and contract workers with the responsibility and obligation to stop work when a perceived unsafe condition or behavior may result in an unwanted event. A key element of a Stop Work Authority Program is a detailed set of written procedures. They will help ensure that every SWA event works consistently and as intended.
A Stop Work Authoring program must clearly define the roles and responsibilities. Examples of roles and responsibilities are:
Stop Work Authority Process (6 Step Example)
Stop Work Authority is a several step process - stop, notify, investigate, correct, resume and follow-up (training on lessons learned etc.)

1. Stop
When an employee or contractor perceives condition(s) or behavior(s) that pose imminent danger to person(s), equipment or environment he or she must immediately initiate a stop work intervention with the person(s) potentially at risk.
If the supervisor is readily available and the affected person(s), equipment or environment is not in imminent danger, coordinate the stop work action through the supervisor. The stop work action should be clearly identify as a stop work action and initiated in a non-combative manner.
2. Notify
Notify affected personnel and supervision of the stop work action. If necessary, stop work activities that are associated with the work area in question. Make the area(s) as safe as possible by removing personnel and stabilizing the situation.
3. Investigate
Affected personnel will discuss the situation and come to an agreement on the stop work action.
If all parties come to an agreement the condition or behavior is safe to proceed without modifications, (e.g. the initiator was unaware of certain information or circumstances), the affected persons should show appreciation to the SWA initiator for their concern and then resume work. The SWA is complete at this point and no further steps are needed.
If it is determined and agreed the SWA is valid, A Stop Work Issuance Form will be completed. The condition(s) or behavior(s) that pose threats or imminent danger to person(s), equipment or the environment must be resolved before restarting work. Work will be suspended until a proper resolution is achieved.
4. Correct
Modifications to the affected area(s) will be made according to the corrections outlined in the Stop Work Issuance Form. The affected area(s) will then be inspected by qualified experts to verify completeness of the modifications and to verify all safety issues have been properly resolved. The completion of modifications will then be noted on the Stop Work Issuance Form.
5. Resume
The affected area(s) will be reopened for work by personnel with restart authority. All affected employees and contractors will be notified of what corrective actions were implemented and that work will recommence.
In the event an employee still believes it is unsafe, they will be assigned to another job with absolutely no retribution.
6. Follow-Up
Operations Managers will provide the root cause analysis to the stop work action and identify any potential opportunities for improvement. The Safety Manager will publish the incident details regarding the stop work action to all Operations Managers and employees outlining the issue, corrective action and lessons learned. Management will promptly review all stop work reports in order to identify any additional investigation or required follow-up.
Depending on your company and reporting structure your specific procedure may vary.
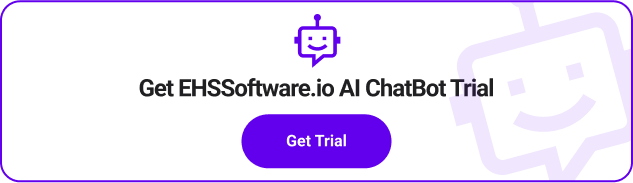
Resources to help reduce accidents
EHSSoftware.io has a successful track record of helping companies reduce incident rates with Safety Audit and Inspection Software, Incident Management Software (e.g. near miss, hazardous conditions, property damage, first aid, injury and illness), Corrective Action Software and Online Safety Compliance Training.
To learn more schedule a 20 minute introductory call consultation.
**** If you found the post helpful please like and share *****
Sources:
1. https://www.osha.gov/pls/oshaweb/owadisp.show_document?p_table=SPEECHES&p_id=2287
2. http://www.ecfr.gov/cgi-bin/text-idx?SID=8422f6fa2f573d1f1acab9dd5eaf65bb&node=10:4.0.2.5.31&rgn=div5
3. http://pbadupws.nrc.gov/docs/ML1408/ML14083A200.pdf