Every successful leader and problem solver understands the importance of uncovering the root cause of a problem. In manufacturing and most other blue collar industries, repeatedly asking 'why' cuts through surface-level symptoms, guiding teams to the underlying issue. The 5 Whys Method of root cause analysis is a valuable tool for modern companies aiming to solve problems effectively and prevent recurring issues.
The concept of finding the root cause of an issue or inefficiency is not a new one. In fact, it originated in the Toyota Production System in the 1930s as Sakichi Toyoda, the company’s founder, worked to fine tune his Lean manufacturing process with a focus on
stopping waste in manufacturing. By encouraging his people to ask “why” repeatedly, he was able to help them find the underlying cause of issues and inefficiencies, improving production and limiting waste.
This focus led others to create the Six Sigma processes, a similar method that focuses on reducing errors, rather than waste. Like the Lean manufacturing method, Six Sigma challenges companies to dig in and find underlying problems. The level of problem-solving required for both models is asking “why?” Thus, both models can use the 5 Whys Method to get to the underlying cause of an issue within a company.
How the 5 Whys Template Works
The 5 Whys Template is a fairly simple process, but it is quite effective. It involves asking “why” five times (or more) until finding the true cause of a problem. First, the person will ask “why” a problem happened and find that cause, and then they will ask why that cause occurred, continuing the process until discovering the true root cause.
While most of the time, five “whys” is sufficient to get to the root cause, this number is arbitrary. Sometimes, more “whys” are necessary, and sometimes, fewer are. The number five is simply a guideline.
Following a Logical, Step-by-Step Approach
The reason the 5 Whys Method works is because of its logical sequence. Someone applying this method will identify each underlying reason in a logical way and then sequentially move to the next reason. By focusing on one variable at a time, finding its underlying cause, and then moving to the next one, you can more quickly find and fix the root cause. The process stops the person from making assumptions or jumping to wrong conclusions but rather encourages step-by-step problem-solving.
When to Use the 5 Whys Template
The 5 Whys Method is effective for simple and moderately difficult problems. It does not work for complex issues or critical thinking problems.
The 5 Whys Method is ideally suited for several industries, particularly those considered "blue collar," where both human error and mechanical problems can come into play when efficiency issues develop. For instance, manufacturing companies need to find problems with workflow or machinery quickly, or production grinds to a halt. Often, implementing the 5 Whys Method can uncover the underlying problem rather than just fixing the symptoms so production can continue. Other industries where this method works well are logistics and warehousing.
5 Whys Example
To understand how the 5 Whys can uncover a root cause, consider an example in manufacturing. Picture a piece of equipment that keeps overheating, stopping production in a busy manufacturing facility. The repair technician needs to use the 5 Whys Method to solve this.
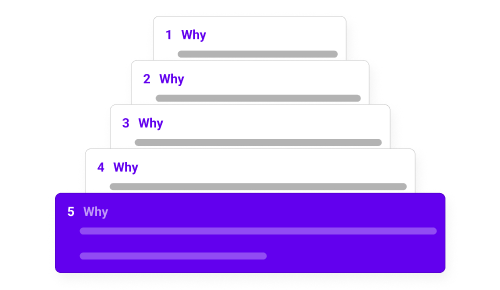
1st Why: Why is the equipment overheating?
The repair professional looks at why the equipment is overheating and discovers that the cooling system isn’t working. However, this isn’t the underlying cause and requires another “why.”
2nd Why: Why is the cooling system not working properly?
The technician discovers that the coolant levels are staying consistently low. While topping them off would fix the problem temporarily, it does not address the underlying problem.
3rd Why: Why are the coolant levels low?
When investigating why the coolant levels are low, the tech discovers that one of the coolant hoses has a slow leak. Fixing this leak would fix the problem, but there is another “why” to ask.
4th Why: Why hasn’t the leak been fixed?
Here, the tech is getting closer to the root cause. Not only does the company need to fix the leak, but they also need to look at their processes to see why nothing has been done about the leak prior to this point. In this example, the tech finds that routine inspections of that particular piece of equipment had not been performed.
5th Why: Why were the inspections missed?
The missed inspections may seem to be the root cause, but there is one more level to explore here. Upon looking more closely at staffing, the technician found that the maintenance team could not keep up with the required maintenance schedule because they were short-staffed. The tech was able to fix the leak and present management with a recommendation to hire some additional maintenance staff or perform scheduling changes to ensure the inspections were completed regularly.
By getting to this root cause, the staffing shortage, the facility was able to take the necessary action to ensure that the inspections were completed more frequently. The end result was fewer leaks left long enough for the machinery to overheat and fewer problems with production stopping.
Advantages of the 5 Whys Template
There’s a reason that a method developed in the 1930s is still taught and used today. That reason is because it works. Some specific advantages of the 5 Whys include the following:

Simplicity
This method is simple to use. It does not require advanced training or specialized tools. Management needs to teach their people to keep asking why until reaching the root cause, and the 5 Whys Method does the rest.

Adaptability
Because the 5 Whys is not a strict set of rules, it can be adapted to apply to many situations and industries. It can be used to dig in and find the root cause of a technical failure with equipment, the underlying human error causing concern, and even problems with a process that are slowing down production and efficiency.

Teamwork
Working through the Whys creates teamwork and collaboration. All team members can collaborate and brainstorm about what is causing the issue. By working as a team, groups can often go even deeper into the “whys” to find root causes.

Cost-effective
Finally, because this process requires no training, external resources, or special tools, it’s one of the most cost-effective ways to solve problems. It is also helpful at reducing inefficiencies and thus can help a company become more productive.
Challenges and Limitations of the 5 Whys
Like any problem-solving tool, the 5 Whys Method is not perfect. Some of the challenges that can occur include:
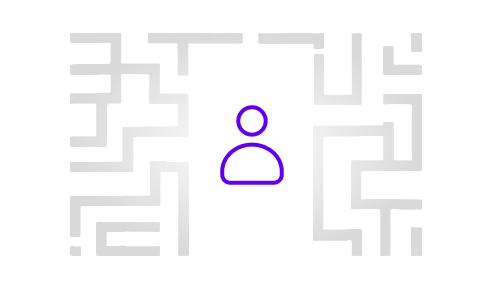
-
Risk of incomplete analysis: You have to keep pushing through the “whys” until you find the root cause. If the facilitator who is implementing this process stops too soon, then the root cause will not be found.
-
Lack of data: If a company implements the 5 Whys Method without sufficient data, the causes may be subjective. This method must be combined with sufficient data to work well.
-
Single root cause focus: Even in simple problems, there may be more than one root cause. Multi-faceted issues often have multiple root causes. The 5 Whys Method makes it easy to focus on just one underlying root cause rather than the option for multiple causes.
-
Facilitation bias: Finally, the person who leads the group through the 5 Whys Method may have a bias about the cause. If the facilitator’s bias drives the questioning, then the resulting diagnosis may be incorrect or incomplete.
How to Effectively Implement the 5 Whys Template in the Workplace
Despite these limitations, the 5 Whys works quite well in many workplaces. However, the way it gets implemented is key to its effectiveness.
First, management needs to form the right team to work through this process. The team needs to include frontline workers as well as supervisors or management, as these individuals are more familiar with what happens on the ground day-to-day. The team members must also be armed with the right knowledge about the organization and its workflows.
Next, the team needs to stay objective. Allowing speculation or bias to creep into the questioning process will make it more difficult to find and fix root causes accurately. Instead, team members need to stick to the facts.
Documentation will help with this. With each “why” asked, the team should keep clear records of what they found. This type of transparency will also create accountability so the overall process works as it should.
Finally, when a root cause is uncovered, the organization should implement the necessary corrective actions to fix it. Simply finding the root cause but not addressing it will not fix the problem fully.
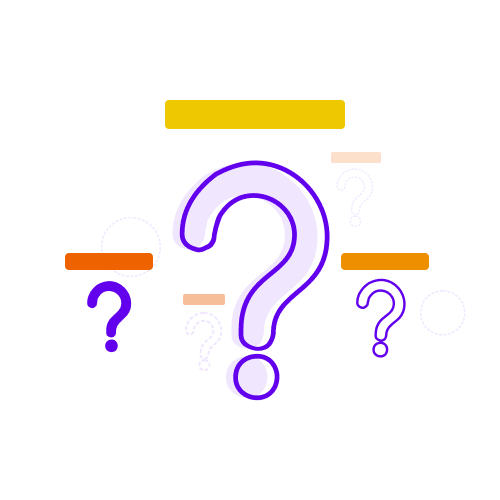
The Role of the 5 Whys Template in Continuous Improvement
To stay competitive, today’s companies need to continuously improve their workflows and efficiency. Several continuous improvement frameworks have risen to the forefront of the manufacturing industry, and the 5 Whys Method fits in perfectly with these. For example, Toyota’s Lean Manufacturing model, which looks at continuously improving inefficiencies, requires finding and fixing those inefficiencies. The model starts with the value of the product and then identifies a value stream for that product. Once that has been mapped, the organization must create flow to get the product and its value to the customer in a timely manner. It also involves pull, which focuses on just-in-time delivery that allows the manufacturer to build products when they are needed and in the right number rather than sitting on endless inventory. Finally, Lean manufacturing works to stop waste in each of these first four steps. That is where the 5 Whys Method comes into the picture.
Using the 5 Whys, manufacturers who want to implement Lean manufacturing can find the root cause of most waste within their organizations. The “whys” give team members the tools necessary to dig in and find the root cause, and so the Lean Manufacturing model can continuously reduce its waste.
Another popular continuous improvement framework is the Kaizen method. Stemming from a Japanese term meaning “change for the better,” this framework focuses on continuously improving operations with the input of all employees to keep a business productive. By teaching employees the 5 Whys Method, manufacturers using the Kaizen method can effectively find areas of improvement.
Start Using the 5 Whys Template Now
The 5 Whys method is a great tool to use to get to the root cause of an issue. It works especially well in blue-collar industries where both equipment problems and human error factors can play a role in inefficiencies. It can also pinpoint inefficiencies in the process itself.
As you look for ways to make your organization more effective, consider teaching your people the 5 Whys Method. It can help you not only solve immediate problems you are facing but also provide the tools to improve your operations over the long term. Finally, it gives you a way to involve your employees in problem-solving so the entire organization can come together to find and fix problems.