When the topic of chemical safety training arises, most of us in the industry immediately think about the 2013 disaster at a Texas fertilizer plant that killed 15 people. The fact is, however, that the risk of exposure to chemicals is present across all industries, and thousands of injuries occur each year.
According to the Occupational Safety and Health Administration (OSHA), more than 50,000 illnesses caused by chemical exposure are reported each year, with 34,000 of those being skin diseases and the remaining resulting in respiratory illnesses.
What about your employees? Do you have chemical safety training procedures in place to keep them protected? While policies may differ between businesses, safety training protocols apply across the board. Consider these four.
1. Personal Protective Equipment
OSHA reports more injuries from skin contamination than breathing contaminated air. Proper PPE, including gloves, safety glasses and clothing must be used to prevent skin exposure.
The National Institute for Occupational Health and Safety (NIOSH), a division of the Centers for Disease Control and Prevention (CDC), provides a valuable resource in its Pocket Guide to Chemical Hazards. You can search its database of recommended protective clothing by chemical to see exactly what is required for the chemicals you will be using. NIOSH also provides access to data on chemical hazards by industry.
Ensure employees know that safety equipment is required and are trained in proper use, storage and maintenance. Further protect employees by properly maintaining eyewash stations, showers, fire extinguishers and first aid kits and make sure all employees know where they are and how to use them.
In addition to safety equipment, laboratory managers must stock only lab equipment that is in good condition. A seemingly insignificant crack in glassware or other storage containers can result in an injury. Use containment trays for additional protection, but help prevent accidents by regularly inspecting lab tools. Have a disposal procedure in place that guarantees a damaged piece of equipment does not return to service.
2. Ensure Clean Air
The CDC has a lengthy list of possible indoor contaminates. Ventilation is one of the most important factor to minimize risk to your employees.
Calculating a safe ventilation rate for your lab can be challenging. Some experts recommend your ventilation system must be capable of handling eight to 10 air change outs per hour when workers are present. However, airflow per hour will vary based on the actual size of your lab.
Global energy leader Seimens compiled a database of Laboratory Ventilation Codes and Standards. Here's the example they used. If your lab is 12 feet by 20 feet, it has a volume of 2,400 cubic feet. One ACH (air change per hour) for that room would equal a ventilation airflow rate of 2,400 cubic feet per hour. Airflow is usually measured by cubic feet per minute (CFM), so you must divide 2,400 cubic feet per hour by 60 (minutes per hour) to get an airflow rate of 40 CFM. Therefore, the Seimens report concludes, "to ventilate a room of 2,400 cubic feet at the rate of 8 ACH would require an airflow rate of 40 CFM × 8 CFM which equals 320 CFM."
That was a mouthful, we know. The point is, however, that it's important to take the time to get it right.
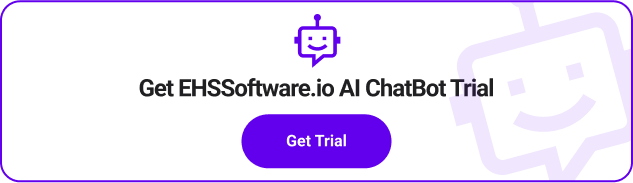
3. Protect Through Organization
Organizing the chemicals used in your company is one of the most important steps you can take to protect employees. Here are a few guidelines to keep in mind when structuring your process.
-
Give every substance a label. Consult the GHS Classification and Labeling Tables. Using industry standards that professionals are familiar with will ensure uniformity and safety.
-
Review labels and keep them up to date.
-
Ensure labels are in good condition.
-
Ensure labels are complete and provide all of the necessary data per GHS requirements.
-
Have a safe system for storage. Depending on the types of chemicals you use, it's likely all substances can't be stored together. However, having an organized storage process will ensure employees can find what they need and incompatible substances don't get inadvertently stored together.
Additionally, stay organized and safe by appointing designated employee(s) to oversee the storage and labeling process. Responsible employee(s) will ensure proper labeling, incompatible substances are never stored together, expired substances are properly discarded and maintain inventory levels. Have an established plan for how new substances enter the workplace. The substance must enter through the designated employee(s), who will ensure all proper handling, storage and disposal procedures are followed.
4. Chemical Safety Training
The best policies and procedures are useless without proper safety training. In addition to emphasizing the guidelines mentioned above, managers must ensure employee safety by outlining procedures that are specific to your environment. Under OSHA's Hazard Communication Standard, employers are required to "ensure chemical safety in the workplace, and information about the identities and hazards of the chemicals must be available and understandable to workers."
Facilitate role play and practice sessions to help employees know exactly how to react to a possible exposure and don safety equipment. Provide practical instruction on laboratory conduct, such as no eating, drinking, or chewing gum. If appropriate, suggest lab workers use the buddy system, always working in the presence of another employee. Implement a training process for all new employees and require that existing employees attend ongoing refresher training.
Chemical safety training is about preventing injuries by unsafe behaviors, minimizing risks and exposure. Regardless of industry or size of company, each employer has the responsibility to provide a safe work environment. The professionals at EHSSoftware.io are experts at training and compliance. Learn more about how our software can help you protect employees, comply with industry standards, and provide effective training while reducing expenses. Contact us to get started.