A manufacturer kept its plant running 24 hours a day, 7 days a week, with two 12-hour shifts. Shortly after a shift change one day a grinder dropped off-line and would not function.
The electrician assigned to repair the grinder arrived shortly thereafter where he entered the motor control room and opened a 2300-volt motor circuit breaker. When he opened the circuit breaker he caused an electrical fault by accidentally contacting energized parts inside the circuit breaker cubicle. The ensuing electric arc burned the employee and ignited his clothing.
Even though he sustained third-degree burns over 60 percent of his body, he was able to depart the motor control room and walk approximately 43 yards to the first aid room. A nearby employee doused the remaining flames with water. Co-workers attended him and two emergency technicians arrived and administered first aid. Emergency medical services arrived within a short time to treat and transport him to a hospital where he was admitted. The electrician died the next day due to the severity of his injuries.
A contracting firm was performing maintenance and repair work for a processing company. The contractors were working on the motor of a Nu Vac 480 volt pneumatic roof-mounted conveyor system. As they were examining the motor, which they found to be running roughly, the motor tripped the electric starter. One of the contractors went to open the Square D 60-ampere standard-duty disconnect switch, which was located in the electrical room on the third floor. When he opened the switch, an explosion and electrical fault occurred involving not only the switch but also a portion of the surrounding electric equipment.
The ensuing electric arc burned the contractor. He was hospitalized with first and second-degree burns to his hand, arm and face. Because of inadequate equipment and housekeeping, combustible cork dust was present throughout the electrical room. Since the combustible dust placed this location in a Class II rating according to the National Electrical Code (NEC), the open-type electric equipment that the contractor operated was unsuitable.
Electrical Safety Case Study Three:
A 30-year-old male electrical technician was assisting a company service representative test the voltage-regulating unit on a new rolling mill. While the electrical technician left the area to get the service manual, the service representative opened the panel cover of the voltage regulator’s control cabinet to prepare for tracing down the low-voltage wiring in question. The wiring was not color-coded and the service representative was not using personal protective equipment (PPE).
The service representative climbed onto a nearby cabinet in order to view the wires. The technician soon returned and began working inside the control cabinet near exposed and energized electrical conductors. The technician began tugging on the low-voltage wires so that the service representative could attempt to identify them from above.
The company service representative heard the electrical technician making gurgling sounds. As he looked down to see the victim, he noticed the victim was shaking as though he were being shocked. Cardiopulmonary resuscitation (CPR) was administered to the victim; however, he was pronounced dead almost 2 hours later. It was determined that he had made contact with an energized electrical conductor.

The following hazard examples can often be attributed to electrical accidents:
-
Not using correct lockout tagout procedures
-
Not using PPE or incorrect use of PPE
-
Equipment not used in proper manner
-
Incorrect equipment used
-
Using faulty equipment
-
Path to ground discontinuous or missing
-
Lack of ground fault protection
-
Improper use of extension cords
-
Accidental live electrical contact (e.g. power lines)
How are such incidents to be prevented? According to OSHA and NFPA 70E workers need the following:
-
Workers need to be able to demonstrate they have the knowledge to do the work they are to do.
-
Workers need to be able to demonstrate they have the skills to do the work they are to do.
-
Workers must receive and understand safety training to recognize and avoid the hazards involved with the work they are to do.
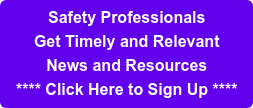